The FT4 Powder Rheometer® is a versatile instrument that can be used in both wet and solid li-ion battery electrode manufacturing processes. The comprehensive powder flow analysis provided can help improve battery efficiency, optimize the electrode packing density, lead to longer battery life, and in wet processes; control slurry agglomerates and dispersibility.
This application note will describe how the FT4 Powder Rheometer® can be used to develop specifications to improve electrode yield for wet processes using a slurry of active material.
Determining Robust Powder Specifications
Lithium-ion (Li-ion) batteries are an advanced technology that will play a key role in the trend toward renewable and sustainable industrial electrification solutions. High energy density, high power density, and long cycle life have driven their adoption and applications in automotive, grid energy storage, and consumer electronics are expected to drive growth even further in the coming years.
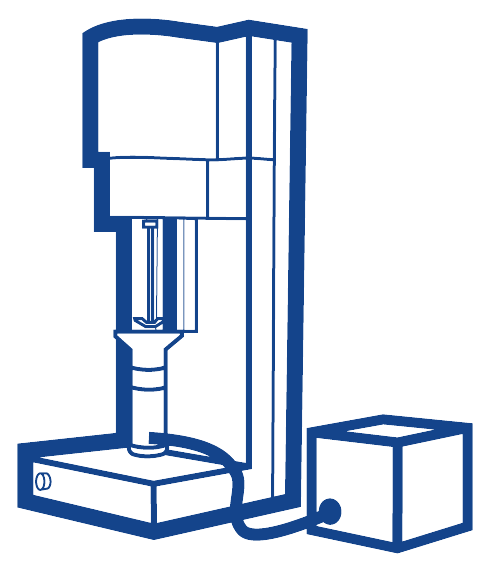
Figure 1 shows a typical manufacturing process for Li-ion batteries. The anode and cathode active materials are processed into a slurry prior to coating, calendaring, and drying steps. These subsequent stages are highly dependent on the quality of the slurry produced at the start of the process.
Slurry characteristics are dependent on the behavior of the active material, binder, and solvents during the mixing process. Some key properties to ensuring a high yield are fineness of grain, viscosity, and solid content. Uniform dispersion of the solid content (active materials) with minimal agglomeration is critical for a high-quality final product.
This application note demonstrates how the FT4 Powder Rheometer® can determine key properties of a battery electrode material, enabling robust powder specifications to be defined.
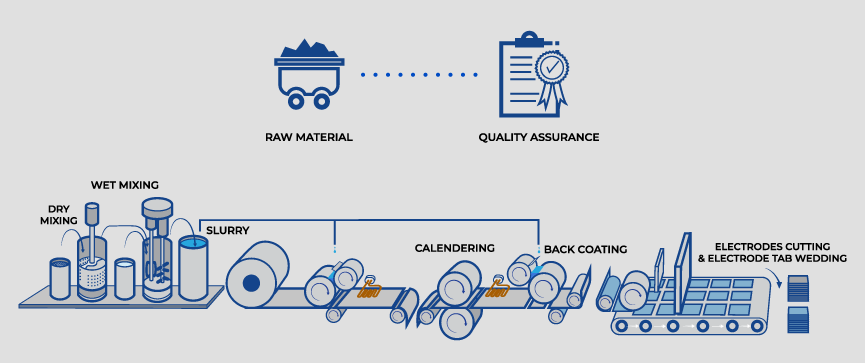
Cathode Powder Characterization Case Study
A common cathode material used in the automotive industry in LiFePO4 (LFP). Even if the chemistry remains the same, minor physical variations in the physical properties of LFP batches can dramatically affect manufacturing performance and yield. In this case study, supplies of LFP from three different suppliers were found to perform differently during manufacturing, resulting in variations in quality and yield. Samples of each batch were analyzed using the FT4 Powder Rheometer® to determine whether rheological properties could be used to specify optimal raw materials.
Two rheological properties that can influence how a powder will mix and disperse are Specific Energy and Permeability
- Specific Energy (SE) quantifies the degree of mechanical interlocking and friction between particles. Lower values are typically associated with more regular, spherical particles.
- Permeability describes the ability of a powder to release or retain entrained air. A higher Pressure Drop value indicates reduced Permeability.
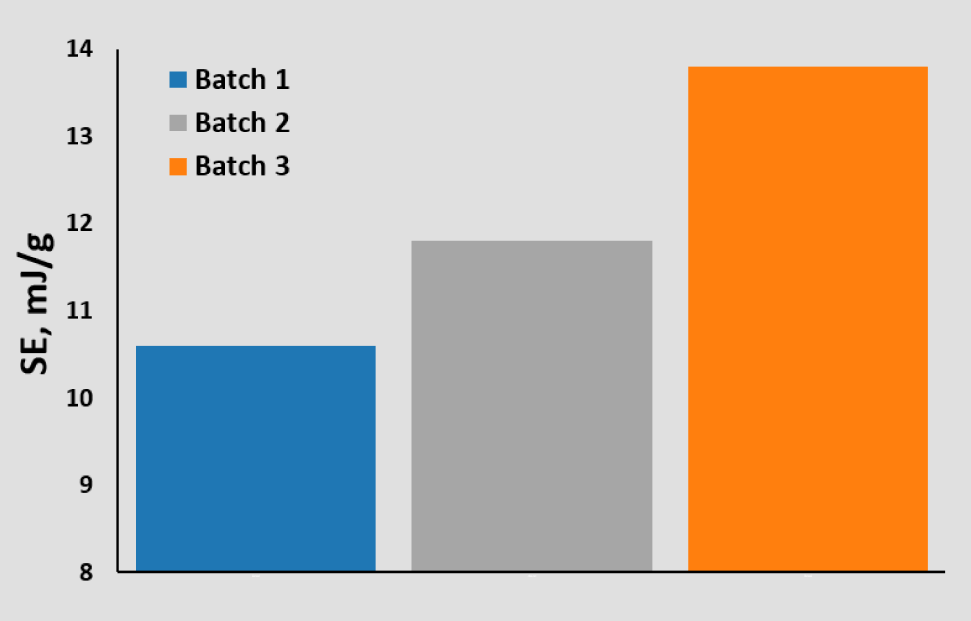
Figure 2 shows the SE values for the three batches. The lower value for Batch 1 indicates reduced mechanical interlocking and friction between the particles. This suggests that the particles are less likely to agglomerate and can disperse more uniformly. Manufacturing experience showed that Batch 1 indeed produced a more homogeneous slurry resulting in higher yield electrode production. Batch 2 and Batch 3 generated higher SE values and in manufacturing exhibited inconsistent performance, including blockages leading to system downtime and out of specification products.
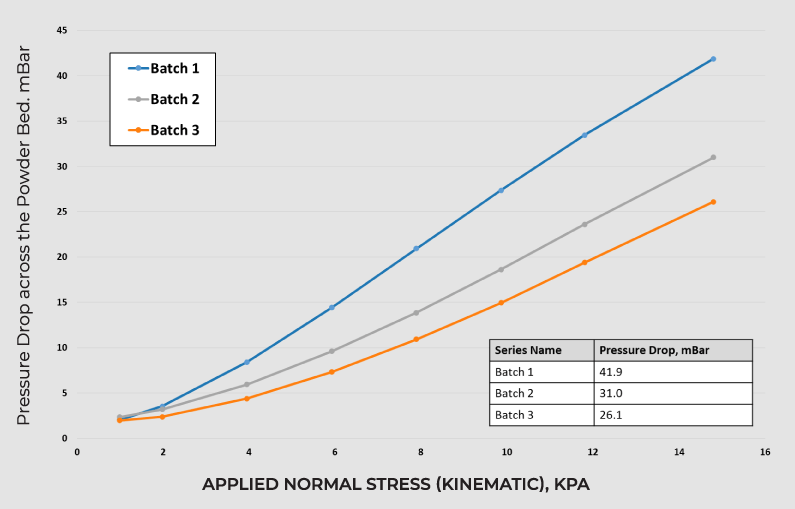
Figure 3 shows the Permeability profiles for the three materials, reported as a Pressure Drop. Batch 1 actually generates the highest Pressure Drop value suggesting reduced Permeability. In this scenario, the higher Pressure Drop is a consequence of an efficiently packed powder bed, which prevents the transmission of air. This is typically associated with materials that can flow and distribute efficiently, reinforcing the correlation observed with process performance and SE values.
Conclusion
The results suggest that less permeable powders, with a low degree of mechanical interlocking and friction are more suitable for the slurry production process, resulting in improved yield. The multivariate approach of the FT4 Powder Rheometer® enables relevant properties to be identified, and accurately quantified, enabling robust powder specifications to be defined.