Introduction
Titanium Dioxide has been used as a pigment and opacifier in a wide range of industries for many years, due to its bright white color and high refractive index. However, despite such widespread use, processing Titanium Dioxide in its powdered form is often extremely challenging due to the powder’s high cohesivity. Special measures often need to be implemented when managing this material in operations such as dispensing from hoppers, feeding into unit operations, and blending with other powders.
Identifying and quantifying which powder properties are conducive to efficient processing allows new formulations to be optimized without the significant cost of running samples through the process to assess suitability, making considerable savings in terms of time and raw materials, and minimizing wastage due to out of specification products.
Assessing Batch-to-Batch Variability
Despite meeting the existing specifications, three batches of Titanium Dioxide demonstrated significantly different behavior when used in the same process, resulting in unacceptable variation in final product quality. A range of traditional characterization techniques were employed but failed to differentiate between the three batches, partially due to the high degree of variability in the test results.
Samples of the batches were analyzed using an FT4 Powder Rheometer®, which demonstrated clear and repeatable differences between them that rationalized the variations in process performance, and enabled the user to reliably assess the quality of incoming batches in process-relevant terms.
Testing Results
Dynamic Testing: Basic Flowability Energy
Sample B generated the highest BFE of the three materials, and Sample C the lowest. High BFE is a consequence of a more efficiently packed powder bed, meaning that the blade is required to displace more powder as it moves and with less available space for particles to move into. This results in more energy being required to mobilize the bed suggests that the powder may be problematic under dynamic, forced flow conditions, such as those experienced in a screw feeder.
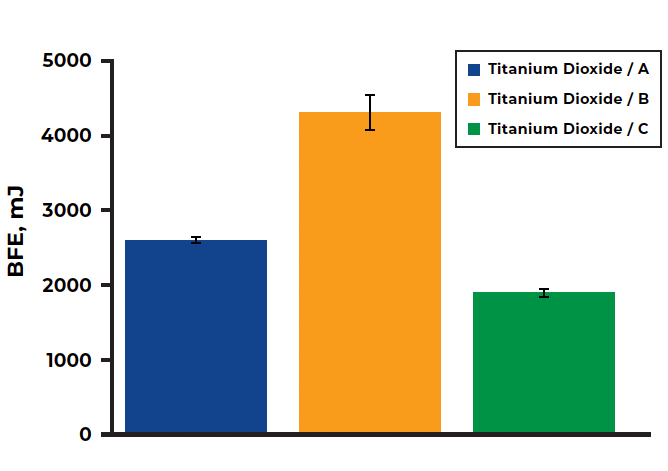
Bulk Testing: Permeability
Sample B generated the lowest Pressure Drop of the three materials, and Sample C the highest. High Pressure Drop indicates a greater resistance to air flow through the sample, i.e., lower Permeability. The lower Pressure Drop (higher Permeability) for Sample B is typical of the uniform structure created by an efficiently packed bed, and is often associated with improved gravitational flow in low-stress environments (such as filling operations).
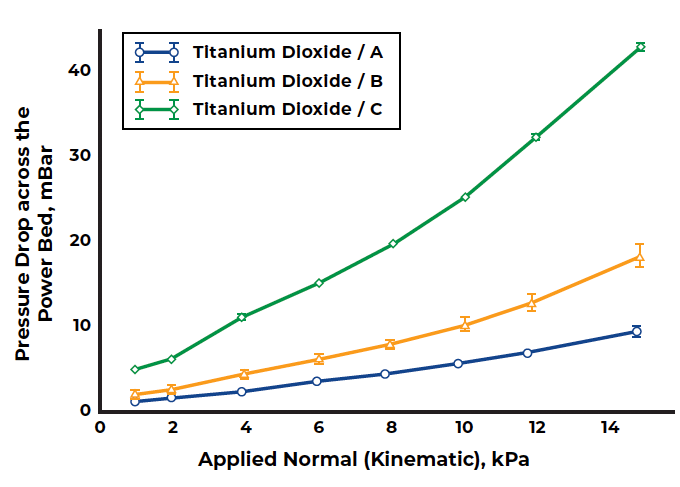
Shear Cell Testing
A different trend was observed in the Shear Cell results, which is a consequence of the different stress and flow regimes established by this test method. Shear Cell tests are intended to represent the high stress, static conditions experienced in operations such as gravitational hopper discharge. Sample A generated significantly higher Shear Stress values than the other two samples, indicating that it is much more resistant to incipient flow (the transition from a static to dynamic state) following storage under consolidation. Samples B and C generated similar Shear Stress values, suggesting that they would perform similarly under these conditions.
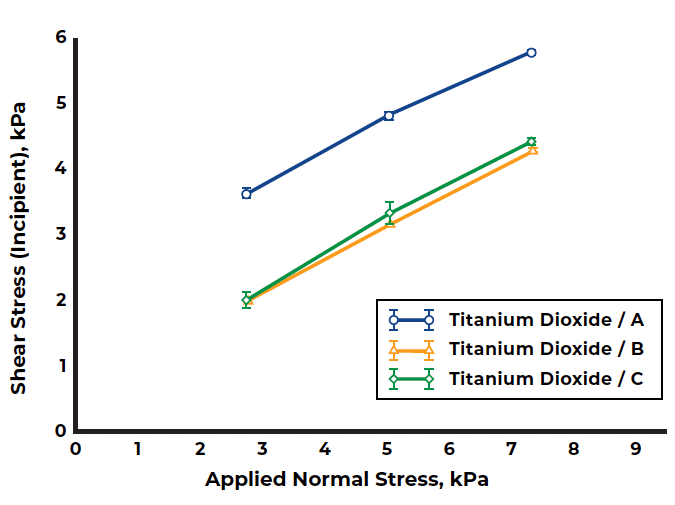
Conclusion
The FT4 has quantified clear and repeatable differences between the three samples in terms of Dynamic, Bulk, and Shear properties. Sample B generated the highest Basic Flowability Energy and Permeability values, and low Shear Stress values, indicating it would perform very differently to the other samples. The results for samples A and C suggest they would exhibit more cohesive behavior than Sample B across a range of processes: Sample C generated the lowest BFE and Permeability values, indicating the most cohesive behavior in lower-stress processes such as blending and filling, and Sample A generated the highest Shear Stress values, indicating that this would present most resistance to flow in high-stress operations such as hopper discharge.
Powder flowability is not an inherent material property, but is more about the ability of powder to flow in a desired manner in a specific piece of equipment. Successful processing demands that the powder and the process are well-matched and it is not uncommon for the same powder to perform well in one process but poorly in another. This means that several characterization methodologies are required, the results from which can be correlated with process ranking to produce a design space of parameters that correspond to acceptable process behavior. Rather than relying on single number characterization to describe behavior across all processes, the FT4’s multivariate approach simulates a range of unit operations, allowing for the direct investigation of a powder’s response to various process and environmental conditions.