Introduction
The properties of dry and damp powders can be as dissimilar as those of chalk and cheese. The uptake of even small amounts of moisture can transform powder properties, making humidity and its impact a critical issue for powder processors. While steps can be taken to control moisture level, by drying the material ahead of processing for example or storing under well-defined conditions, the cost-effective application of such measures relies on identifying when they are truly required. Inadequate humidity control may be a major source of process inefficiency, but unnecessary control simply adds expense.
There is a widespread misconception that any moisture worsens powder properties, but in practice all materials respond differently. This article examines efficient methods for quantifying the impact of humidity and presents illustrative data for limestone and microcrystalline cellulose, two very different industrially important powders. The results show how multi-faceted powder characterisation gives comprehensive insight into the effect of moisture uptake, providing a sound basis upon which to develop effective strategies for humidity control.
Tools for Powder Characterization
A first step when assessing how humidity impacts powder processing performance is to identify analytical techniques that generate relevant and appropriate data. There are many different powder testing methods in use but for process optimisation studies it is most productive to focus on those methods able to generate sensitive, reproducible data that correlate reliably with process performance.
The refinement of certain traditional powder testing techniques, such as shear and bulk property measurement, through the use of modern instrumentation and methodologies, have made them more reliable and reproducible, and consequently more informative for this type of study. More recently however, the development of dynamic powder testing has brought with it the ability to perform a range of complementary tests that provide more detailed information about powder behaviour.
Dynamic characterisation involves measuring the axial and rotational forces acting on a blade as it traverses through a sample along a fixed helical path. The resulting flow energy values are a direct quantification of powder flowability. Highly sensitive dynamic characterisation has the distinct advantage of allowing the measurement of powders in consolidated, conditioned and aerated, or even fluidised, states, so enabling the direct investigation of the impact of air.
The following experimental study illustrates how measuring a range of powder properties supports the development of a detailed understanding of the very different responses to moisture exhibited by limestone [BCR116, European Commission] and microcrystalline cellulose (MCC) [PH200, FMC].
Comparing the Impact of Humidity on MCC and Limestone
The amount of moisture both absorbed and adsorbed by powders varies enormously. For powder processors, however, it is the way in which that moisture affects powder behaviour that is often most critical. In tests to compare the impact of humidity on both MCC and limestone, the sorption properties of the two materials were observed to be very different, with MCC taking up an order of magnitude more water than the limestone, when allowed to equilibrate in environments of controlled relative humidity. However, as subsequent testing showed, the behaviour of both materials was significantly altered by their exposure to moisture.
Figure 1 shows a collection of dynamic and bulk data that illustrate how the behaviour of the limestone and MCC vary as function of moisture. These data were all acquired using an FT4 Powder Rheometer® (Freeman Technology, Tewkesbury, UK), a highly automated powder tester that incorporates dynamic, shear and bulk test methodologies. [1,2]. Ref 1 provides a full description of the methodologies applied. Collectively these data quantify the impact of humidity in a process relevant way. Furthermore, they support the development of a rationale for the behaviour observed.
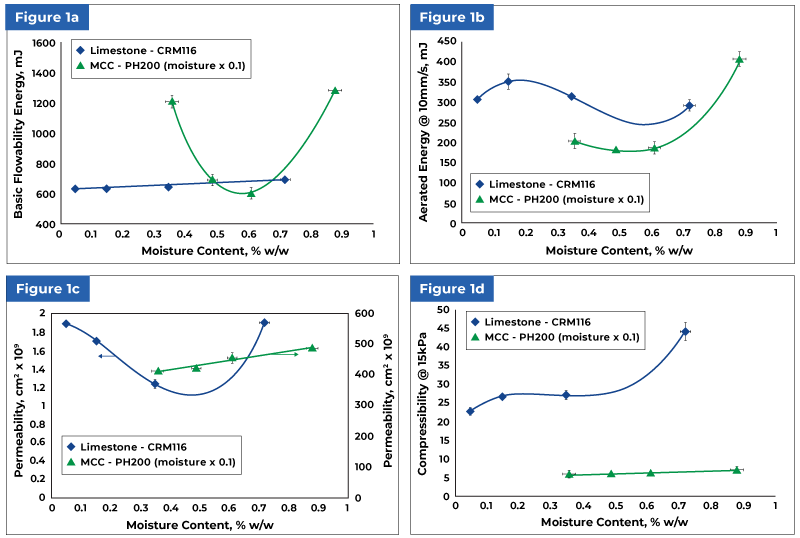
Note: The moisture content values for MCC are an order of magnitude greater than for the limestone.
Microcrystalline Cellulose
In Figure 1 the two curves showing dynamic data for MCC – for basic flowability energy (BFE) and for aerated energy (AE) – although quite different, echo one another in terms of exhibiting a minimum flow energy. Both therefore indicate that moisture improves the flow properties of MCC up to a certain point, beyond which there is a deterioration in flowability.
During the study, it was noted that the MCC sample coated the inner wall of the glass storage vessel prior to testing, suggesting a tendency towards electrostatic charging, and providing insight as to why the powder might display the behaviour it does. If the high BFE value for the drier sample arises from electrostatic interaction between the particles then increasing moisture level could cause a reduction in BFE by discharging the sample.
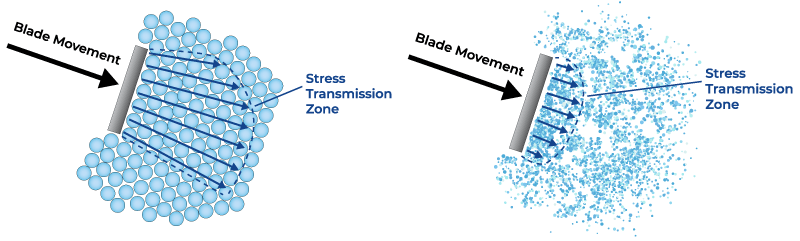
The steady increase of BFE above a certain level of moisture is a more commonly observed pattern and is attributable to the material adsorbing sufficient moisture to begin to agglomerate due to increased adhesion and capillary forces between particles. Large particles, or agglomerates, can present significant resistance to the kind of compacting flow pattern applied in BFE testing, and therefore are often associated with high BFE values when compared with finer, more cohesive powders whose structures contain more void spaces (see Figure 2).
During aeration testing, the ability of the air to separate particles, and reduce flow energy, again depends on both the electrostatic forces and mechanical adhesive forces acting between them. However here, it is clear that agglomeration has a more marked influence on behaviour, as a result of the agglomerate’s higher mass, larger size and increased adhesive forces. The different shapes of the two dynamic curves are therefore both explained by the idea of sample discharge and subsequent agglomeration.
This formation of agglomerates results in large void spaces within the powder bed, a trend reflected in the steady increase in permeability observed in bulk property testing. Beds with large particles and substantial voidage, although difficult to fluidise, present relatively low resistance to air flow and are therefore associated with higher permeability.
Compressibility on the other hand, and indeed bulk density (data not shown), changed very little across the range of moisture contents studied, suggesting that, with this powder, packing behaviour is not an important factor with respect to the changes induced by humidity. This highlights a limitation of using bulk density measurements to infer information about changes in flow behaviour, as these two parameters may, or, as in this case, may not directly correlate. Shear test data (not shown) for this material were similarly insensitive to the changes induced by increasing moisture content, further emphasising the need to choose optimal test strategies for any given investigation.
One final important note to make about the MCC is that it exhibits these changes in flowability and other parameters over a range of conditions that are industrially relevant, across the 25-50% Relative Humidity range that could easily represent ambient conditions. This suggests that MCC could readily exhibit variable flow characteristics when handled in an industrial setting.
Limestone
With a particle size of just 4 microns, the limestone sample is a much finer, more cohesive powder than the coarser (180 microns) MCC. For limestone, the two sets of dynamic data are at first sight inconsistent, a steady upward trend in BFE and variability in aeration testing. However, a look at the scale of the permeability graph for limestone indicates why aeration testing may have produced such data.
The limestone has very low permeability because of its fine particle size. Although permeability appears to change with moisture content, in absolute terms these changes are very small, with permeability being extremely low at all moisture levels. This means that the limestone samples will substantially resist aeration and that upward flowing air will tend to channel through to the surface, rather than promoting steady fluidisation. Therefore the introduction of air has a limited and variable impact on flow energy, with the extent and influence of channelling varying erratically with moisture content.
Returning to the BFE data, these show a steady upward trend with moisture suggesting that water is making the limestone more adhesive, acting as a binder, forming liquid bonds and creating small agglomerates. Turning to the compressibility data, even minor changes in moisture content appear to have a significant effect, compressibility increasing steadily with moisture content, a trend that is entirely consistent with this proposition of increasing agglomeration.
In general, more cohesive powders tend to be associated with high compressibility values. This is because the high interparticular forces between cohesive particles promote the formation of loose agglomerates that entrain air, thereby creating a bed that can be significantly compressed. In less cohesive powders, on the other hand, the particles can move more easily with respect to one another and tend to pack closely, making further compression of the bed difficult. Bulk density is similarly influenced by particle packing which is why increases in cohesivity are also often associated with reduction in bulk density. In these tests the bulk density (data not shown) of the limestone did indeed decrease progressively with increasing moisture content, a result that is consistent with a steady increase in the amount of air trapped in the bed and increasing compressibility.
As with the MCC, the shear data gathered for limestone (not shown) reflected this overall trend in flow behaviour. However, again as with the MCC, other parameters more sensitively quantified the impact of humidity on the properties and therefore, in this instance, represented a more suitable choice for the study.
Conclusion
To accurately manage the impact of humidity on process performance it is crucial to quantify and understand how adsorbed moisture affects powder properties. This experimental study of MCC and limestone illustrates how the measurement of certain dynamic and bulk property data can provide the necessary information and underlines some important issues for those investing in powder testing strategies to investigate this issue.
Firstly, the data show that the sorption properties of a material are not a reliable indicator of the extent of associated changes in powder properties. Even if a material takes up relatively small quantities of moisture, as is the case with the limestone, important powder properties such as compressibility and permeability can be transformed.
Secondly, the results demonstrate the effectiveness of a multi-faceted approach to powder characterisation since it is in combination that the results reveal the full story of exactly how the moisture is affecting the powder. And finally, the study presents some firm data that dispels the idea that all moisture is detrimental to powder behaviour. For example, the flowability of the MCC improved with increasing moisture content under certain conditions, possibly because of the ability of the water to dissipate accumulated electrostatic charge.
What is clear is that small changes in moisture content can have a significant effect on powder behaviour, even with hydrophobic powders, giving rise to effects that are neither linear nor predictable. Appropriate testing strategies are therefore essential, for those wishing to truly understand the effect of humidity on powder processing.
References
- Freeman R. “Measuring the flow properties of consolidated, conditioned and aerated powders – A comparative study using a powder rheometer and a rotational shear cell”, Powder Technology 174 (2007) 25-33.
- Storage and flow of solids, Bulletin 123 of the Utah Engineering Experiment Station, November 1964 (Revised 1980), A.W.Jenike, University of Utah.