Cohesive Behaviour
Cohesion is regularly regarded as one of the most influential properties to bulk powder flowability and is often blamed for powder processing issues. In a cohesive powder, particles attract to each other to form clumps or agglomerates that can cause blockages and inconsistent feeding and dosing, leading to wastage and inefficient processing. Cohesive powders can show great variability in their bulk density, being prone to packing inefficiently or loosely under gravity, but they can also form tight structures with high compact strength when compressed, posing challenges to feeding and filling operations and to their general management in manufacturing lines.
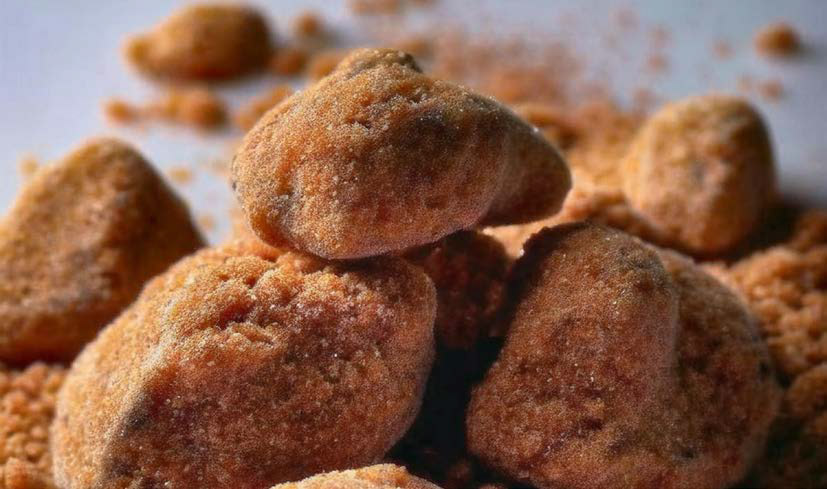
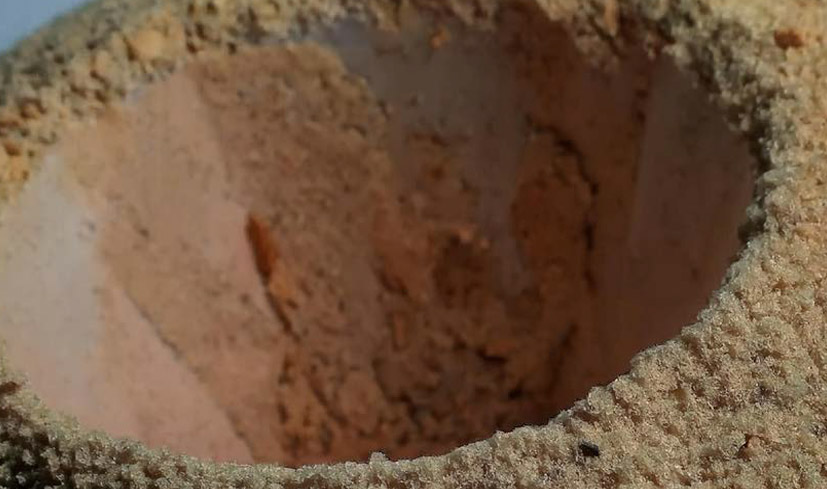

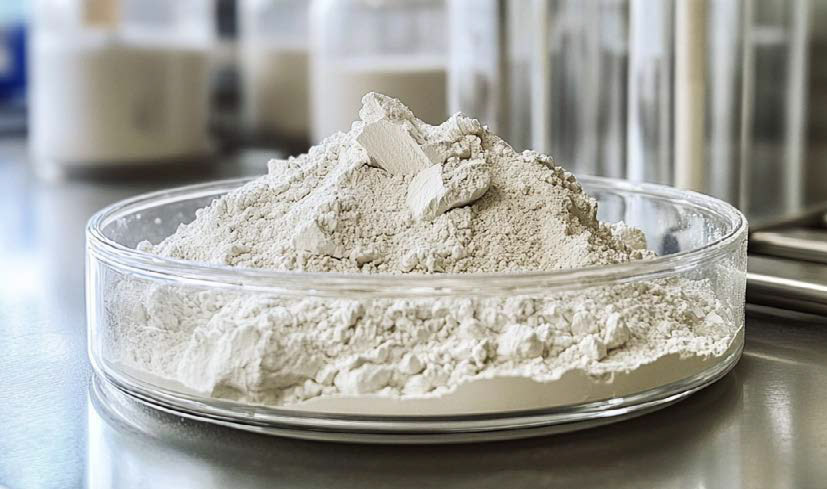
Characterising powder cohesivity means quantifying the likelihood of encountering certain handling and manufacturing problems, and assigning a number to the quality of a powdered product. Understanding the extent to which cohesive forces affect powder flowability allows the prediction of a material’s performance in a process without the need to mimic each stage directly, and informs the powder formulators or handlers on how to address flow problems due to cohesion, for example by modifying particle size, chemistry or via surface treatments.
Cohesive Forces
Cohesion is the name given to the combination of all the forces of attraction between particles, including van der Waals, liquid bridging and electrostatics. However, whether a powder will behave cohesively is determined by how relevant these attractive forces are compared to the other forces acting on the particles.
Gravity is a force that is always present and acting in favour of particles moving over each other, but particles will only be able to fall past each other and into gaps if their weight is larger than the net attractive (cohesive) forces holding neighbouring particles together. If particles have low mass, because they are small or made of a low-density material, cohesive forces may be strong enough to hold particles in place relative to each other, providing a structure for loose packing and enabling the formation of clumps where particles are arranged in a seemingly solid lattice
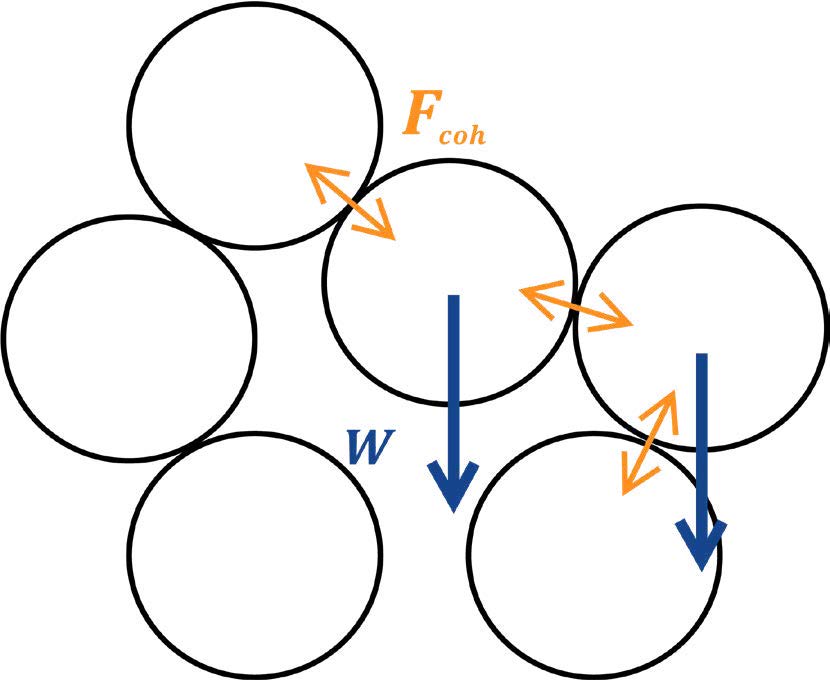
Powder cohesivity then, is not determined just by the absolute strength of cohesive forces, but by how strong they are compared to the average particle weight. We can quantify cohesive behaviour as the ratio
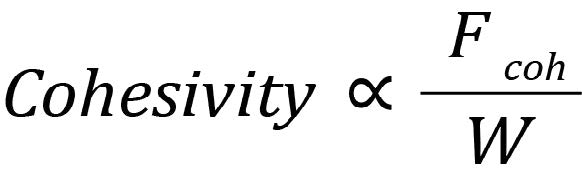
where the larger the ratio F coh/W > 1 implies the powder is more likely to show cohesive behaviour such as loose packing, high bulk density variability and clumping. A ratio F coh/W < 1 suggests that the attractive forces between particles don’t play a significant role in how they move past each other, but it is worth noting that this does not mean the powder is free-flowing: even if a powder is non-cohesive, other forces such as friction and interlocking between particles because of their shape can stop particles from moving smoothly past each other.
The Influence Of Particle Size
There is a common misconception that powders with small particle size distribution (PSD) have stronger cohesive forces, but this is not necessarily the case. In fact, the types of forces classified as cohesive (van der Waals, liquid bridging and electrostatics) are typically surface forces that depend on the type and area of contact between particles, rather than on the particle volume.
Rather, because smaller particles have a smaller mass, cohesive attractive forces can hold particles in place more firmly. For powders of similar particle density, shape and surface properties, a smaller average particle weight W skews the ratio F coh/W towards larger values, corresponding with a more cohesive behaviour.
The images below show a limestone powder separated into batches of different particle size but comparable size distribution span (PSD width/ median size). The samples were milled from the same block of raw material and stored under the same environmental conditions, so their composition and particle shape and surface properties – and therefore the average absolute interparticle cohesive force – are likely to be similar for all samples. However, as the mean particle size (and weight) decreases and the ratio F coh/W increases, we also see a marked increase in the cohesive behaviour of the powders.
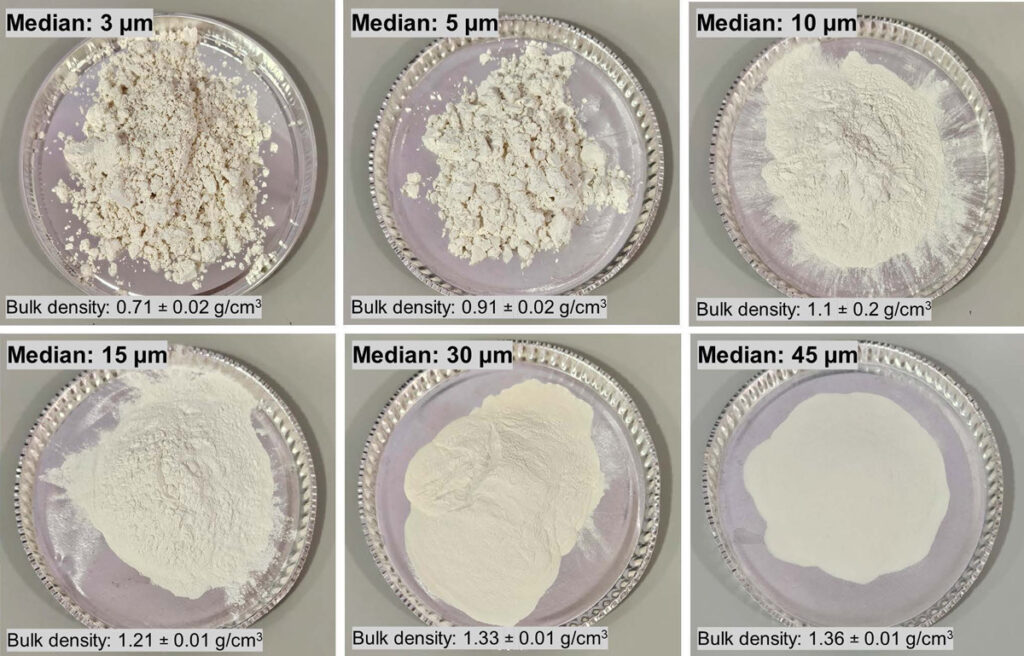
With larger particle size, the surface of the powder heaps becomes noticeably smoother, with visibly less clumps, and we also measured the bulk density to increase as particles arrange more efficiently under gravity.
Even though it is likely all samples have similar strengths of interparticle surface forces related to van der Waals, electrostatics and the moisture content, the role they play, that is how relevant these cohesive forces are to the overall powder behaviour and flow properties is very different!
How to measure powder cohesivity
Three measurements of the FT4 Powder Rheometer are especially well-suited to identify strongly cohesive behaviour.
A high Conditioned Bulk Density (CBD) is associated with cohesive behaviour that locks bulk conformation in place before achieving optimal packing. Powder Compressibility under an external load then demonstrates that a more ideal packing is achievable when compressive forces exceed cohesive forces. Finally, fluidization is the separation of particles from one another to allow air to pass; the force of air required to fluidize the bed is an indication of the cohesive forces holding the particles to one another.
These FT4 measurements inherently average the properties of all interparticle interactions in a sufficiently large bulk. As such, the cohesivity of a powdered material can be characterised independently of other measurements such as particle size, shape or surface properties.
Conditioned Bulk Density and particle packing
When cohesive forces are stronger than the average particle weight, they can hold particles in place and prevent them from falling into gaps between other particles. As a result, the bulk will contain a high proportion of empty space.
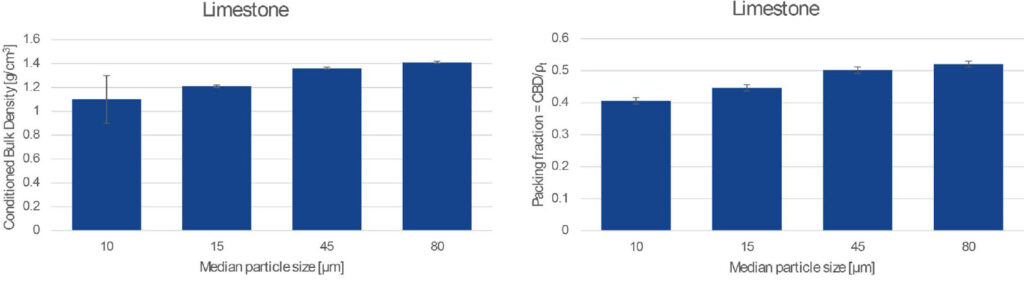
When comparing powders with similar skeletal density, and similar particle size distribution span, a higher cohesivity (higher F coh/W value) manifests as a lower Conditioned Bulk Density. Moreover, if the skeletal density is known (see Accupyc), the fraction of the bulk volume occupied by solid particles can be found. The solid volume fraction indicates particle packing efficiency and it is higher the lower the cohesivity of the powder.
For Bulk Density to be a helpful metric of powder cohesivity, it must be assessed under precise initial packing conditions, which can be difficult to achieve. The unique Conditioning protocol of the FT4 imposes a repeatable loose packing state; this ensures that observed differences in conditioned bulk density are due to difference in inter-particle cohesion, not differences in pouring or scooping actions.
Compressibility
Cohesive forces tend to lock particles in position before the bulk achieves an optimal packing state. The application of an external load can overcome cohesive forces to achieve a more optimized packing state.
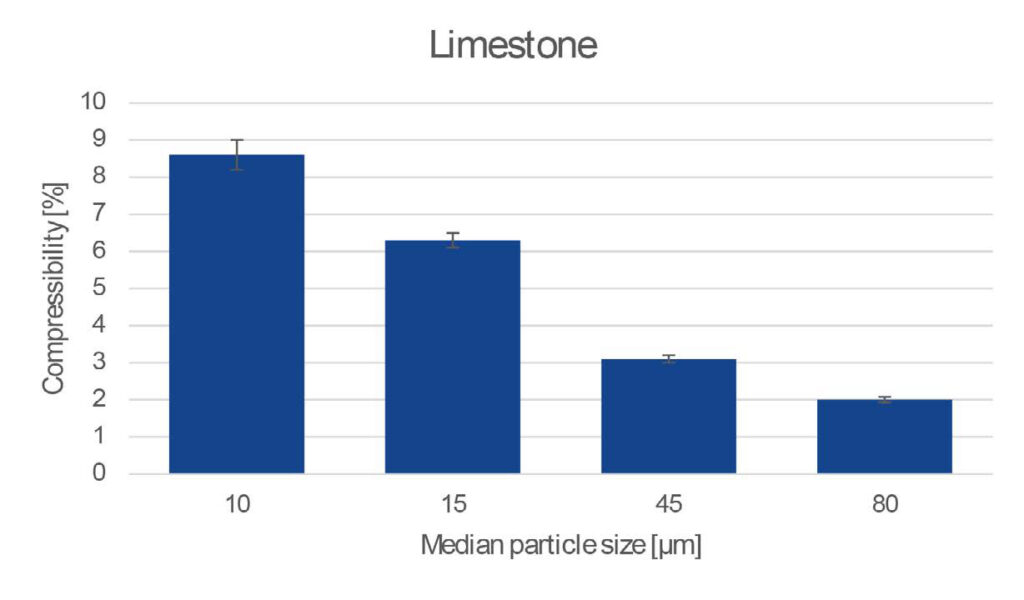
Measuring the difference in volume between the gravitationally-packed and compressed states provides a value for the powder Compressibility. As more cohesive powders tend to contain a larger proportion of empty spaces between particles, the bulk contains more space for particles to rearrange into when a comparatively large external load compresses the powder.
It is worth noting that particle shape (interlocking) and surface properties can also affect particle ability to fit into gaps, and therefore the proportion of empty spaces between particles. When using bulk properties such as density and compressibility to evaluate sample cohesivity, we must be careful to consider how different shape and surface properties are between the samples being compared.
Aeration and Fluidization
Cohesive forces arrest particles in non-ideal packing states and can also restrict the ability of particles to separate from one another. The force required to separate particles from one another can be evaluated by air flow across the powder bed. The FT4 Powder Rheometer with Aeration Control Unit (ACU) introduces air at precise flow rates through the base of a column of powder, and measures the pressure drop and dilation of the powder bed. When air flows through the sample at a high enough speed, the upwards drag can separate and suspend particles individually to achieve a state of full fluidization.
Powder fluidization occurs when there is a balance of fluid-dynamic forces (air drag) to gravitational and cohesive forces. When air speed is high enough, the drag can overcome both the average particle weight and the cohesive forces holding particles to one another, and at this point the powder bed expands such that particles are suspended by the air stream.
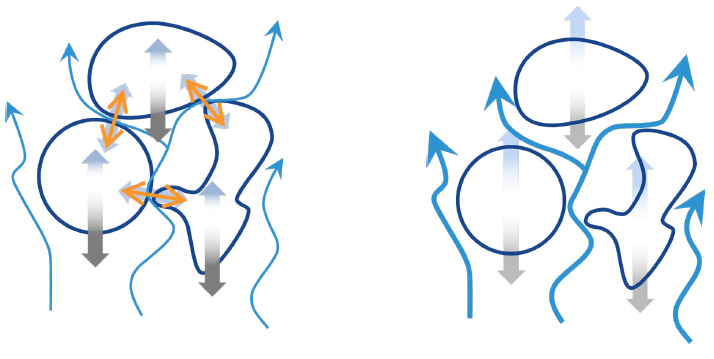
If cohesive forces are very large, air drag must be significantly higher to achieve fluidization. In some cases, where F coh/W >> 1, most particles remain in contact with one another; high air speeds separate some particles and form a small number of channels through the powder bed. These channels divert the applied air flow and the powder does not achieve fluidization at all.
We see, then, that powder ability to achieve full and uniform fluidization depends on the relative magnitudes of air drag (which is equal to the bed weight at fluidization) and interparticle forces, that is
F coh/W. Because the action of the air is of lifting and separating particles, it is the net cohesive (attractive) forces that prevent fluidization, with minimal influence of other forces such as friction and mechanical interlocking
Cohesive vs free-flowing
It is important to remember that cohesive forces are only one group of forces that define powder flow behaviour. Cohesive forces inhibit particle separation and prevent smooth gravity-driven flows. Therefore, low cohesivity is a requirement for a powder to be called free-flowing, but even materials that are non-cohesive may show issues during processing if their frictional and/or interlocking properties are significant.
This is especially true when considering powder behaviour in processes that include multiple regimes of shear and compressive stress. The relative magnitude of these process forces can influence the relative importance of powder flow characteristics. For example, extruders tend to involve high compressive and shearing forces, for which interparticle friction will more significantly affect flow than cohesive forces. In contrast, lean phase pneumatic conveyers achieve desirable performance when particles are easily separated and suspended in an air stream; cohesive properties dominate this flow and will determine process characteristics while frictional forces will exert only a minor influence.
Comprehensive powder flow characterisation requires a complete understanding of all forces preventing the smooth movement of particles past each other in a range of processing conditions. The multivariate approach of the FT4 Powder Rheometer makes it the ideal instrument to simulate a range of unit operations, allowing for the direct investigation of a powder’s response to various process and environmental conditions.