Filling is a common operation across all industries, although fill weights and tolerances vary widely. The pharmaceutical industry often requires milligram doses to be filled accurately and at high speed, in order to meet the stringent criteria and high throughput requirements of tablet manufacture. By contrast, the bulk chemicals and minerals industries may load powders into 20 ton containers, employing a much longer filling process and without the regulatory pressures governing accuracy.
The factors that influence filling efficiency will depend on the type of equipment being used. Some systems are purely gravity driven, whilst others rely on force-feeding. In many applications, such as tablet manufacture on a rotary press, the powder fills the dies through a combination of gravity and force-fed flow. The influence of each of the two mechanisms will depend on the geometry of the feedframe, the flow rate through the press and the characteristics of the powder. It is easy to see, with wide variation in each of these variables that this is a complex process and remains challenging to model from knowledge of a limited number of particle properties and process parameters.
At large scale, such as filling of bags or bulk containers, the process might be volumetric filling or one based on mass. In both cases it is typical that augers or rotary valves directly attached to the bottom of the feed hopper are employed. In this configuration, the factors that control filling efficiency may be different to those in tablet manufacture, however, efficiency across all scales and in all processes will depend on the compatibility of the material properties with the conditions imposed in the processing environment.
Die Filling
In this example of a typical die filling process, the filling “shoe” moves relative to the stationary die, as opposed to the die moving underneath the feedframe, as in a rotary tablet press. There are many geometries and configurations, but in all cases there is a common objective – to fill the die in a homogeneous manner, in a time frame that enables the target throughput to be achieved.
In the example, powder is discharged from the hopper into the filling shoe. The shoe then moves laterally across the top of the die and powder flows into the empty cavity below. This particular configuration is gravitationally induced and involves relatively low stress, as there are few forces consolidating the powder in the shoe. By contrast, in a tablet press feedframe the stresses will be higher as the feedframe paddles force powder to circulate on top of the table. The consistency of flow of powder into the feedframe will influence the stress in the powder as it circulates, as will the speed of the feedframe relative to the turret speed. As this can be set independently, it is possible to configure the feedframe to generate a range of dynamics and stress conditions, simply by altering its speed relative to the turret. The effect is to adjust the amount of forced flow that contributes to flow into the die, and also from where in the feedframe the powder exits into the die. Changing the shape of the paddles is one method of managing the extent to which forced flow, rather than purely gravimetric flow, contributes to the filling process.

As with all powder processing, it is necessary to consider the compatibility of the powder with the process conditions. A successful outcome, in this case consistently achieving target fill weight, depends on the characteristics of the powder suiting the conditions imposed by the process. Whether gravity, force-fed, or a combination of both, predicting performance can only be achieved by understanding the process conditions and measuring the relevant powder characteristics.
The goal of the process is to uniformly fill the die with powder, without entraining air within the bulk, leading to low weight variation and high content uniformity in the resulting tablets. By contrast, a poorly filled die will contain agglomerates that entrain air, leading to higher weight variation, risking low content uniformity, and likely leading to delamination (‘capping’) of the tablets when air entrained within the bulk is first compressed by the tablet press, and then expands within the body of the tablet.
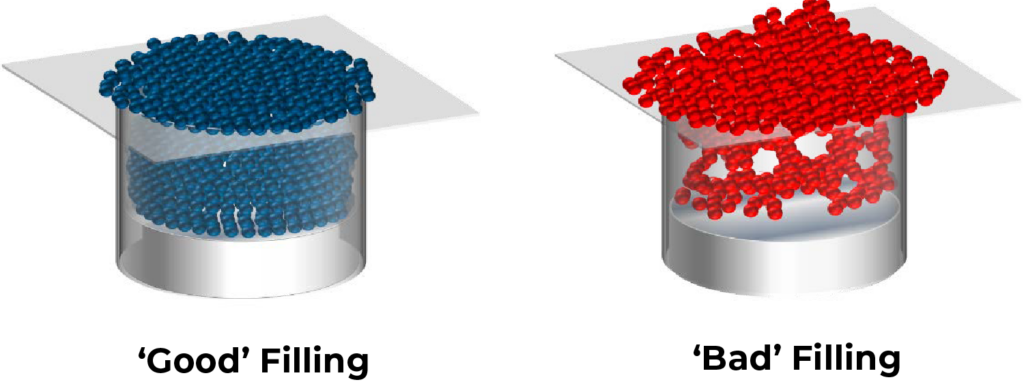
Quantifying the Mechanisms that Influence Filling
Several mechanisms of particle interaction will strongly influence filling efficiency.
Cohesive Forces
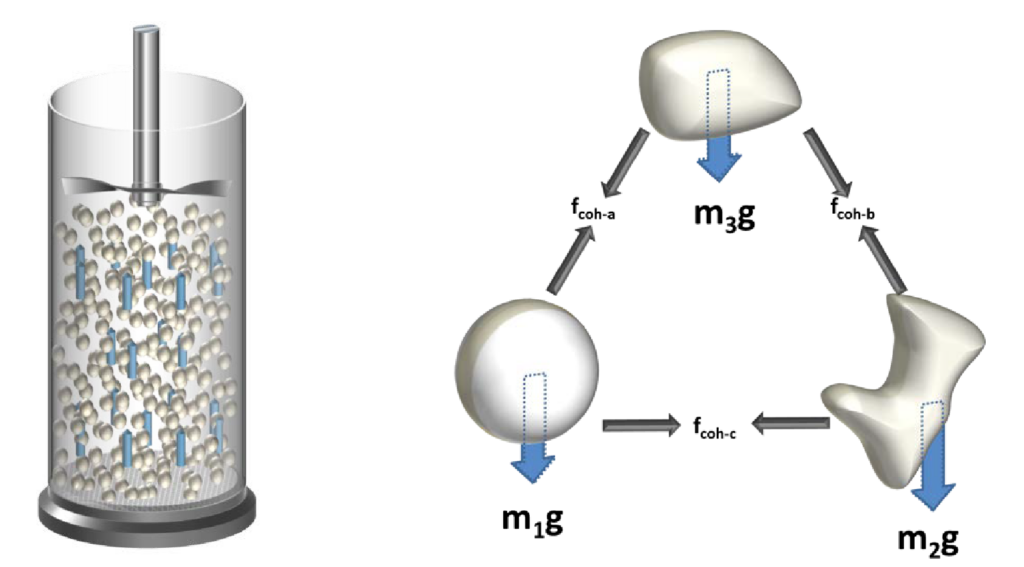
Adjacent particles attract one another as a result of electrostatic, Van der Waal’s and covalent forces. Particles are unable to move independently of their neighbours and agglomerates may form. The result is to reduce filling efficiency.
The FT4 Aeration test can quantify the extent of these attractive forces between the particles. The method first measures the energy needed to establish flow in a conditioned powder (the Basic Flowability Energy, BFE), and then compares it to the energy measured whilst establishing the same flow pattern, but this time whilst air is being passed through the powder column (Aerated Energy, AE). In powders with low cohesion, particles are bound weakly to their neighbours and can move independently of one another. When air is introduced to such powders, it is able to pass between each particle so that the entire bed becomes fluidised. In this state, there is little or no particle-particle contact and the AE is reduced to almost zero. Conversely, cohesive powders tend to form agglomerates, preventing the bed from becoming substantially aerated by channelling the air through a single or reduced number of pathways, leading to less change in the packing structure. The AE will reduce to some extent compared to the BFE, but values of AE are likely to remain high.
Mechanical Friction and Particle Interlocking
Particles of irregular shape and/or with rough surface texture will tend to lock together and form temporary mechanical bridges. The resulting effect is to limit the flow of powder into the die, even if the die is mostly empty.
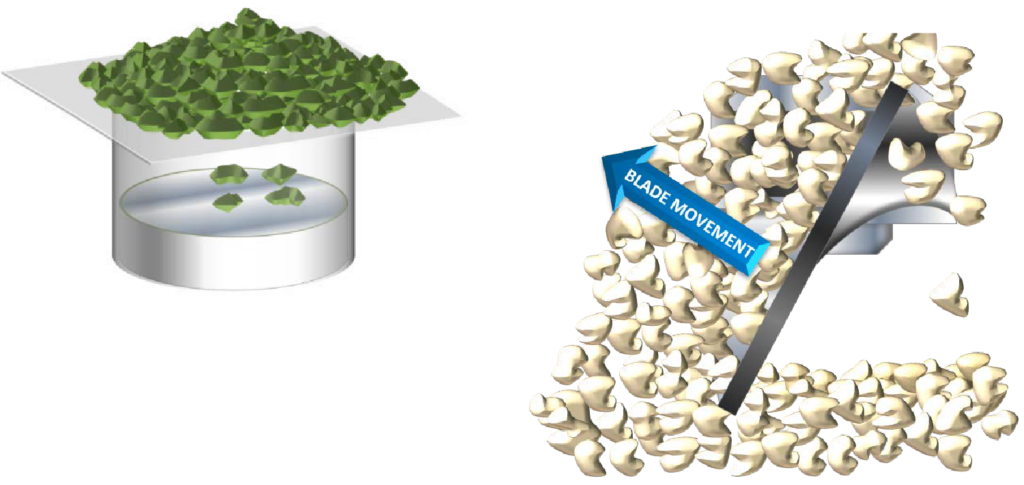
Specific Energy (SE) is derived from a dynamic test that measures the resistance of particles moving relative to one another in an unconfined state. The blade moves from the bottom of the powder bed to the top (in contrast to the BFE and AE measurements making the tests very sensitive to inter-particular interlocking and friction. The lower the Specific Energy, the lower the mechanical interlocking, and the more likely the powder is to flow under gravity in an unconfined state.
Permeability
Permeability is a measure of the ease with which air can move through a powder. In most configurations, air is required to flow between particles in order to exit the die. Low permeability typically results in intermittent flow and compromised filling.
Permeability is quantified by measuring the pressure drop across the powder bed while air is introduced to the bottom of the powder column at a constant velocity. A vented piston holds the powder in place while still allowing air to pass through the bed and easily escape. The piston can also be used to consolidate the powder, measuring pressure drop as a function of consolidation. The air pressure at the top of the powder is considered to be zero (or atmospheric pressure). The air pressure measured at the base of the powder column represents the resistance of the powder to air flow for a given consolidating load and air velocity.
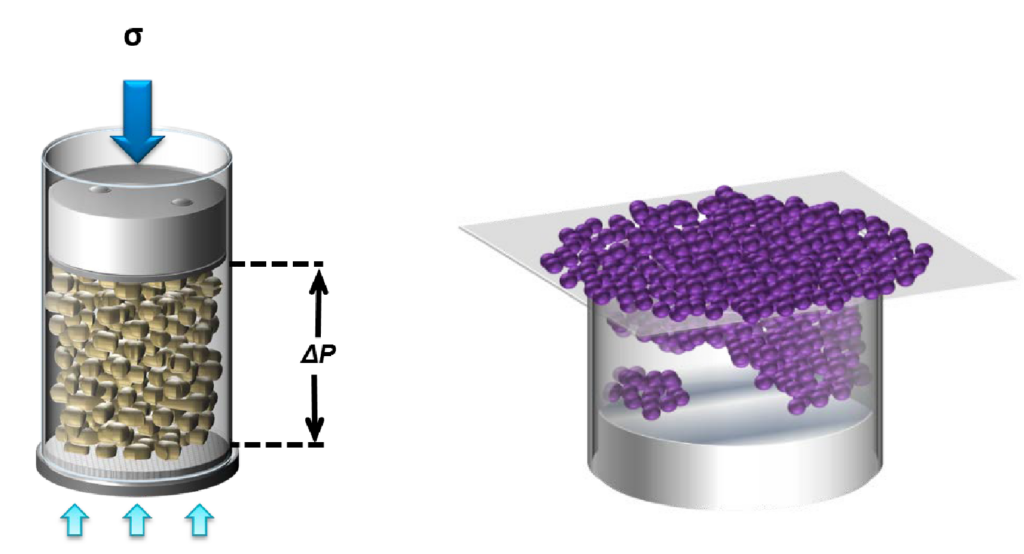
Quantifying Filling Performance
This example die filling process involves a shoe containing powder moving at a controlled velocity relative to a fixed die. Filling Ratio was calculated as the mass of powder in the die after filling, compared to the mass if the entire volume of the die had been filled with a material of the powder’s bulk density. A ratio of 1.0 represents complete die fill, whilst a value of 0.2 indicates that only 20% of the die has been filled.
Four materials were chosen, with known but differing particle sizes and shapes. For each material, experiments were completed over a range of shoe speeds.
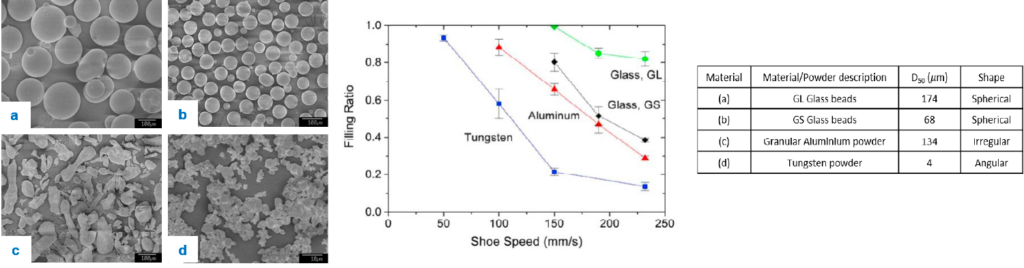
Tungsten showed the worst performance in the operation, as it was unable to achieve a 100% fill at even the lowest shoe speeds, and barely filling at all at the highest shoe speeds when compared to the other powders. Conversely, the Large Glass Beads were the most effective at filling the die, achieving 100% fill at even moderate shoe speeds. The Small Glass Beads and Aluminium showed moderate performance, achieving over 75% fill of the die, but requiring the shoe to move more slowly in order to do so.
FT4 Powder Rheometer Test Results
Dynamic Testing: Aeration
Tungsten generated the highest AE of the samples, indicating it was the least sensitive to aeration. By contrast, the three other samples all generated a very low AE, indicating that they could be fully fluidised. Low sensitivity to aeration is an indicator of higher cohesivity, as the strong inter-particular forces prevent the air from passing between all of the particles, leading to a non-uniform aeration of the powder.
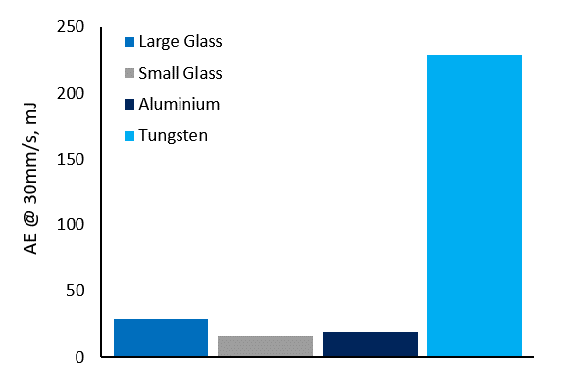
Dynamic Testing: Specific Energy
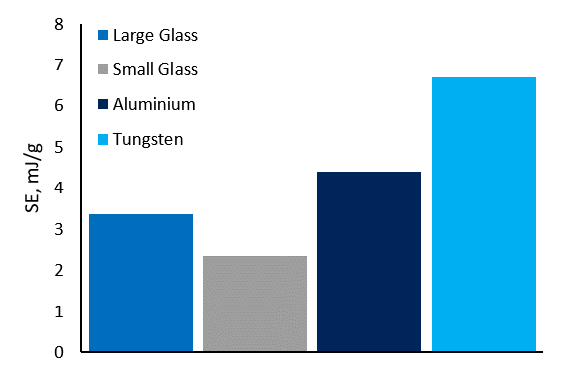
Tungsten generated the highest SE of the samples, indicating a high degree of mechanical interlocking and friction and further suggesting more cohesive behaviour. By contrast, both Glass Bead samples generated a low SE, however the Small Glass Beads generated a lower SE (lower inter-particle interlocking) than the Large Glass Beads, despite the Large Glass Beads filling the die the most effectively.
Bulk Testing: Permeability
The Large Glass Beads generated the lowest Pressure Drop Across the Powder Bed, indicating the highest permeability. The Small Glass beads generated a considerably higher Pressure Drop (PD), indicating lower permeability and that entrained air will take longer to escape after falling into the die with the powder. Tungsten generated the highest Pressure Drop of all, indicating the lowest permeability. Low permeability is often associated with cohesive behaviour in a number of operations.
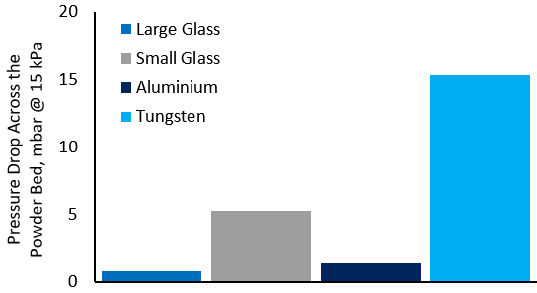
Constructing the Design Space
By combining the data collected using the FT4 Powder Rheometer and Filling Ratio, it is possible to construct a design space for predicting process performance.
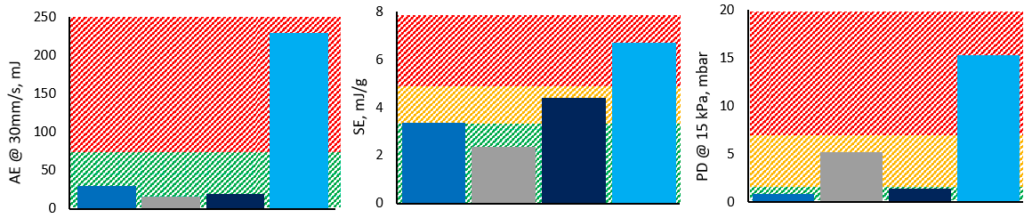
Large Glass Beads were shown to exhibit good performance, so their properties can be used to define acceptable values for each parameter, (coloured green in each graph.) Conversely, Tungsten exhibited poor performance so its properties can define the limits of unacceptable values, (coloured red on the graphs.)
Powders which exhibit intermediate performance can be used to fine-tune the design space, particularly where multiple criteria must be met. For example, Aluminium generates similar AE and PD values to Large Glass Beads but exhibits considerably worse performance. This is likely to be due to the higher SE value so helps define an acceptable limit for SE. Similarly, Small Glass Beads generate low AE and SE values but a higher PD value contributes to worse performance, defining a limit for this value as well.
If a new formulation or blend is to be used in this process, by assessing its properties prior to operation, process performance can be determined, and incompatible formulations can be identified. If the properties lie in the ‘green’ zone in each test, it can be expected that this powder will perform well in the filling operation, generating a high fill ratio comparable to the Large Glass beads. If the results lie in the ‘red’ zone, the powder is likely to perform very poorly in the operation, and prove problematic under any applied conditions. Samples in the ‘red’ zone can be screened out of the process before they enter it, preventing poor filling performance, increasing productivity and reducing waste. If a result lies in an intermediate or ‘amber’ zone, performance may be acceptable, if not optimal, and may be improved by adjusting process parameters accordingly.
Conclusion
The Dynamic and Bulk characterisation techniques of the FT4 Powder Rheometer have demonstrated clear and repeatable differences between four samples known to behave differently in process. The results also demonstrate that individual techniques may not be sufficient to fully describe the process performance, and that a multivariate approach is required.
The tests show that powders with a high sensitivity to aeration and low degree of cohesion (low AE), a relatively low degree of mechanical interlocking and friction (low SE) and a high permeability (low Pressure Drop) perform best in this operation. Conversely, powders with lower sensitivity to aeration, greater particle interlocking and lower permeability are likely to prove more problematic. The data also show that permeability is a highly influential parameter, meaning that powders with less than optimal dynamic flow properties (such as the Large Glass Beads) still perform most effectively in this process. This approach to process understanding enables a design space to be defined, against which new materials can be assessed to predict performance.
Powder flowability is not an inherent material property, but is more about the ability of powder to flow in a desired manner in a specific piece of equipment. Successful processing demands that the powder and the process are well-matched and it is not uncommon for the same powder to perform well in one process but poorly in another. This means that several characterisation methodologies are required, the results from which can be correlated with process ranking to produce a design space of parameters that correspond to acceptable process behaviour. Rather than relying on single number characterisation to describe behaviour across all processes, the FT4’s multivariate approach simulates a range of unit operations, allowing for the direct investigation of a powder’s response to various process and environmental conditions.