Introduction
A degas study was conducted to determine the effectiveness of flow versus vacuum degas. An amorphous silica-alumina and a microporous zeolite were prepared by both techniques and then nitrogen isotherms were collected for both materials. The resulting isotherms established equivalence between vacuum versus flow degas.
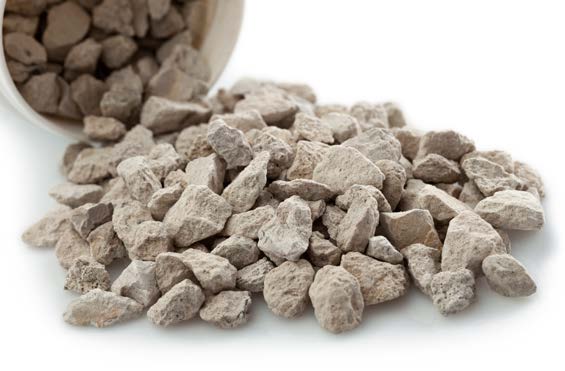
Theory
Typical degas options include vacuum or flowing degas. The basic concept of degas is quite simple. The sample material is placed in an inert environment. This inert environment exploits chemical potential and creates a favorable state for an adsorbed molecule, perhaps water or carbon dioxide to shift from an adsorbed state to the inert environment. We can justify this theory by assuming a finite concentration of adsorbed molecules on the surface versus zero concentration in the inert environment. This assumption allows us to use Le Chatelier’s principle which establishes that the equilibrium must shift. Hence the adsorbed molecules will change concentration (desorb) to reach a new chemical equilibrium.
To assist the shift from the adsorbed molecule to an inert environment, the temperature of the surface may be increased. Increasing temperature will increase the rate of desorption. This establishes two key requirements of degassing:
- Inert environment – shift from
adsorbed phase to inert. - Heat – increase the rate.
Vacuum vs. Flowing Degas Methods
In the present study we accept that temperature may be controlled by various methods and that commercial temperature controllers provide repeatable performance. Rather than studying temperature control, this document will evaluate the topic of vacuum versus flowing degas.
- Vacuum degas utilizes mass action as the only method for shifting the chemical equilibrium. An adsorbed molecule has a concentration on the surface, C and a negligible pressure, P=0 in the vapor phase. The pressure is maintained near zero since the sample is in a vacuum. Heating the sample increases the rate of transfer from the adsorbed molecules to the inert environment.
- Flowing degas also utilizes mass action by constant inert purge. The desorbed molecules are swept from the system via the continuous inert gas flow and the partial pressure of the desorbed molecules in an inert stream approaches zero in a manner similar to the vacuum technique. Heating the sample also increases the rate of desorption. However, the inert purge method also has another driving force.
For example, nitrogen or helium molecules are continuously striking the surface of the material. During this process, momentum from the molecules striking the surface is transferred to adsorbed molecules. The inert gas method benefits from additional energy input and, as a result, a faster rate of degassing.
Analysis
Based on these fundamental actions of vacuum and flowing degas, we can assume that both techniques provide a comparable result. An amorphous silica-alumina and microporous zeolite (13X) was used to explore the various degas options available to gas adsorption instrument users.
To establish the performance of both degassing techniques, a sample of silica alumina was prepared using the matrix of instruments and degas given in Table 1.
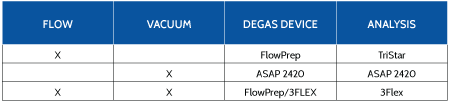
Nitrogen isotherm data were collected and the results are presented in Figure 1. This simple study
establishes the equivalence of flow versus vacuum degas options for non-microporous materials.
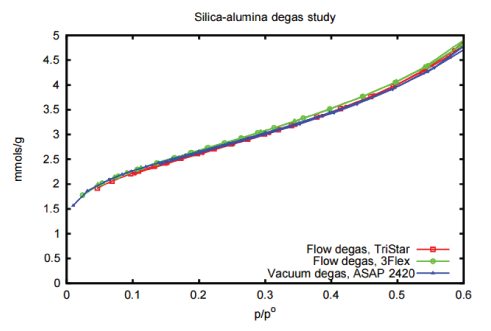
The study was then expanded to investigate the use of flow versus vacuum degas and demonstrate the utility of a secondary on-port degas to establish an ultra clean sample prior to adsorption analyses.
The micropore zeolite was chosen because of the nature of these materials to adsorb small quantities of stray gas. The results of this study are presented in Figure 2.
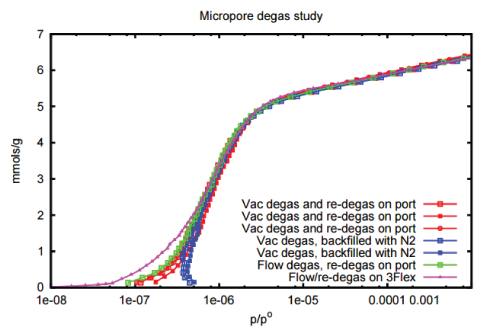
The isotherms collected using nitrogen and the 13X demonstrate two clear trends:
- Flow degassing or vacuum degassing combined with on-port degassing provides the highest quality isotherm.
- Vacuum degassing does not provide the same high quality result as vacuum degassing plus a subsequent on-port degas.
Conclusion
Either flow or vacuum degassing provides a clean surface for adsorption. This conclusion is established by comparing the nitrogen isotherms obtained on an amorphous silica alumina and the 13X zeolite. The addition of on-port degas provided an ultra-clean sample devoid of any stray gas, weakly sorbed molecules, or molecules that are diffusion limited and difficult to quickly remove from the surface. On-port degassing also eliminated any possibility of contamination arising from transport of the sample from degas to the analysis station.
External Sample Preparation units available from Micromeritics:
FlowPrep 060 – The FlowPrep applies both heat and a stream of inert gas to the sample for removable of adsorbed contaminants from the surface and pores. With six degassing stations, this sample preparation unit lets you choose the temperature, gas, and flow rate best suited for your sample material and application. Needle valves allow the user to introduce the flowing gas slowly to prevent fluidization of samples.
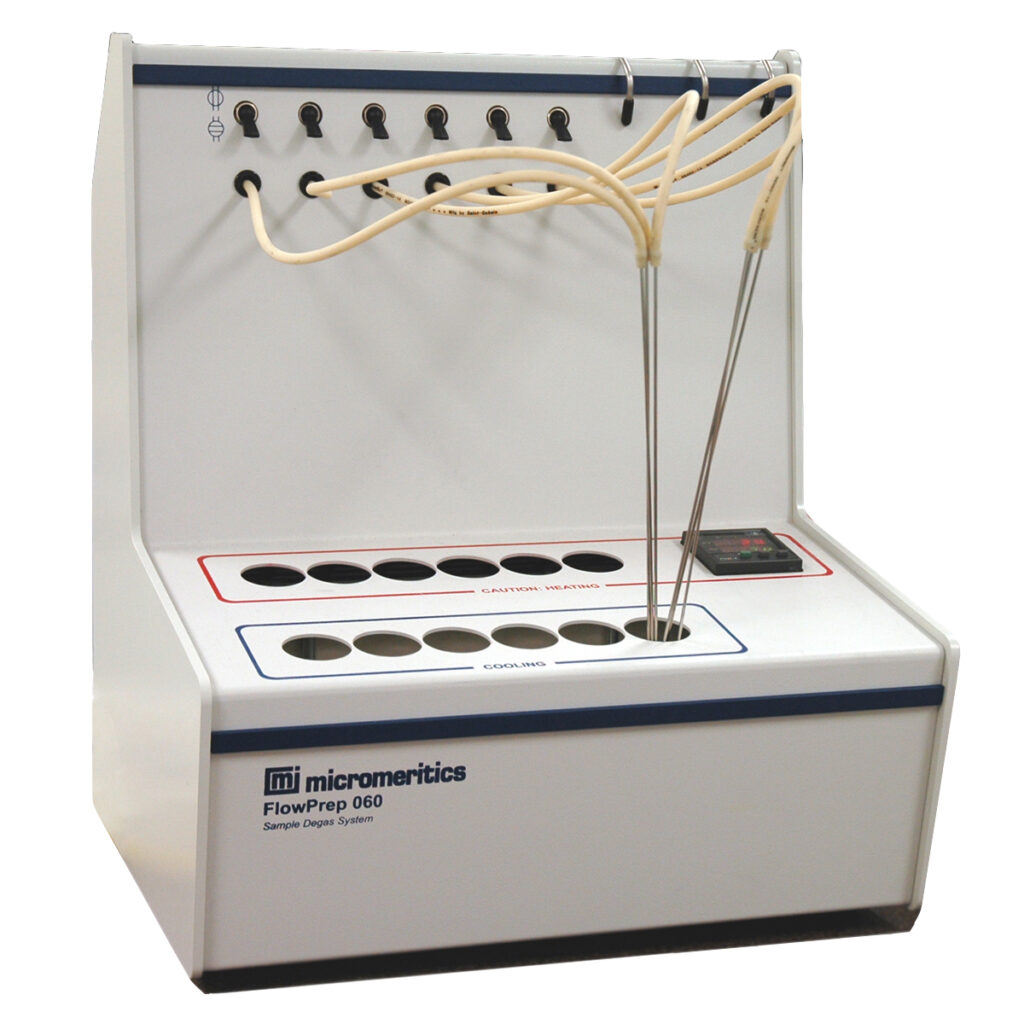
VacPrep 061 – The VacPrep offers two methods for removing adsorbed contaminants. In addition to flowing gas, this sample preparation unit provides vacuum to prepare samples by heating and evacuation. The VacPrep offers the user a choice of vacuum or gas flow on each of the six degassing stations. Needle valves allow the user to introduce the flowing gas or vacuum slowly to prevent fluidization of samples.
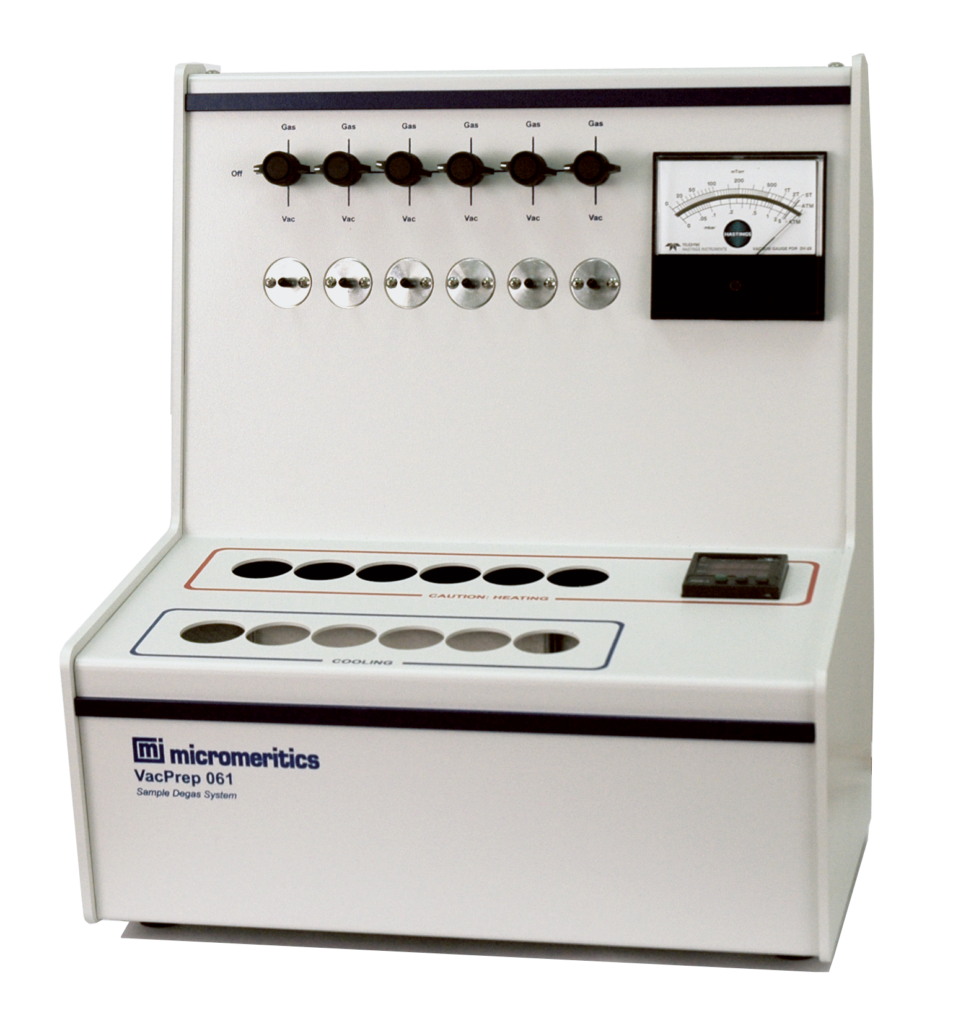
SmartPrep 065 – The SmartPrep applies a stream of flowing gas over the sample at elevated temperatures to remove adsorbed contaminants. Temperature, ramp rates, and soak times are individually controlled on the six degassing stations by a computer. This sample preparation unit contains two serial ports, one for connecting to the computer and the other for connection to an additional SmartPrep. Up to five ramps and soaks are allowed. All degas information is integrated into the sample data file for future reference.
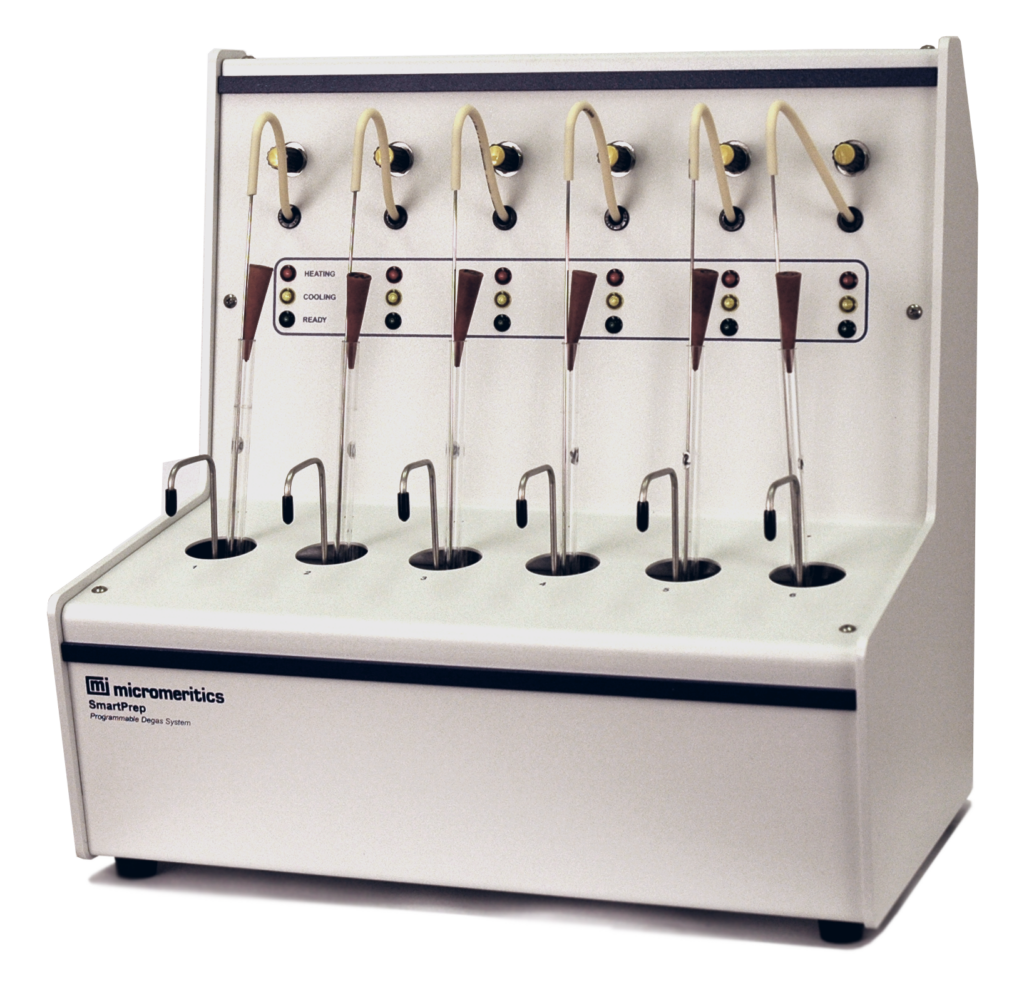